Understanding the Essential Role of Red Line Sight Glass in Modern Business
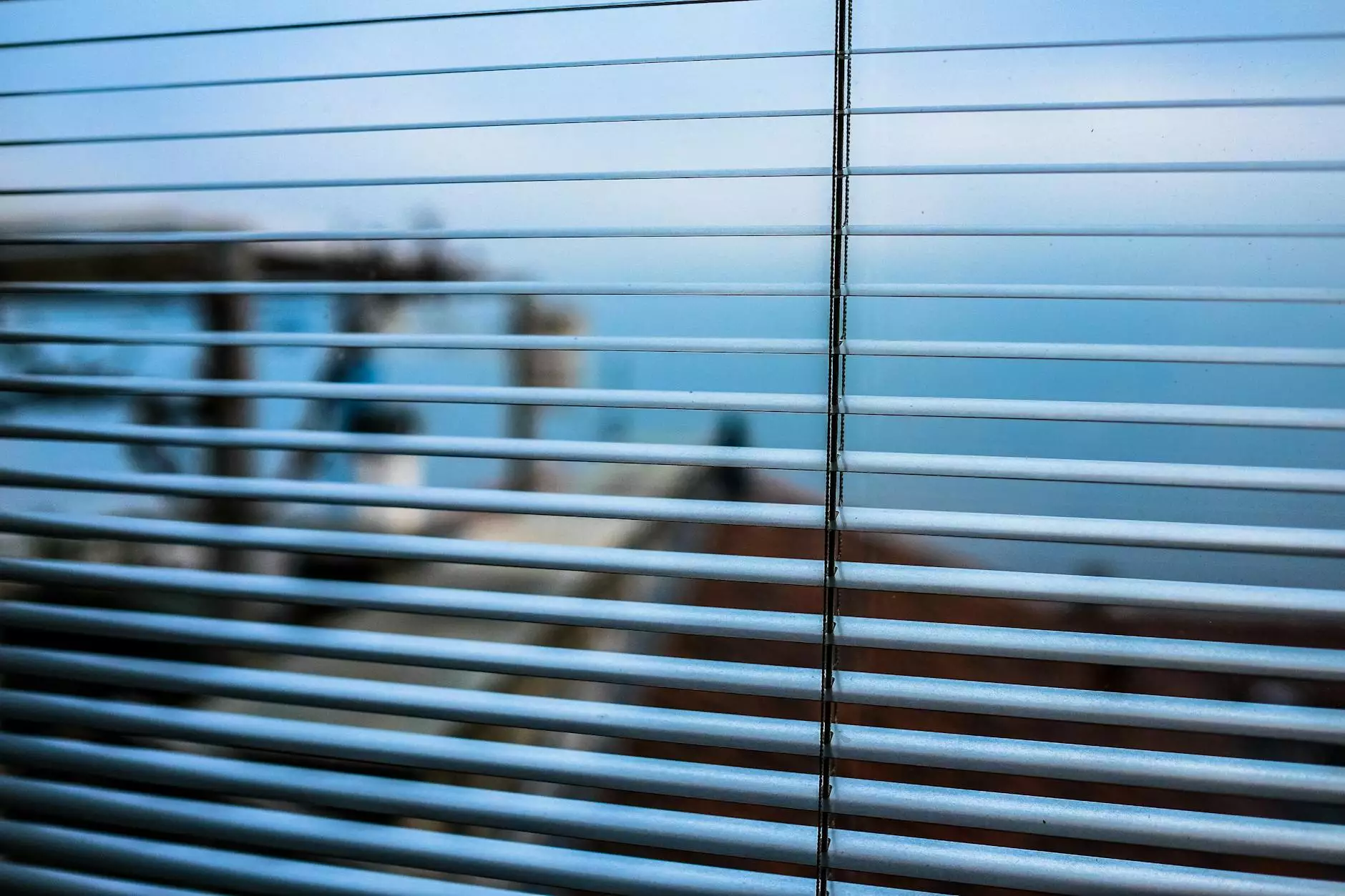
In the world of industry, red line sight glass serves as a crucial tool for monitoring, managing, and enhancing operational efficiency. This article delves deep into the intricacies of red line sight glass, its applications, importance, and maintenance—especially relevant for businesses in the Home & Garden, Glass & Mirrors, and Fireplace Services sectors, like gage-glass.com.
What is Red Line Sight Glass?
A red line sight glass is a transparent tube that is used in various applications, primarily in industrial and commercial settings. It allows operators to observe the level of liquids or gases within a system, which is critical for processes involving fluid management. Typically made of robust materials such as borosilicate glass, these sight glasses are designed to withstand high pressure and temperature variations.
Why is Red Line Sight Glass Important?
In sectors where monitoring fluid levels is critical, the red line sight glass provides a visual indication that can prevent major accidents and equipment failure. It simplifies the process of gauging the amount of fluid in a tank or pipeline, delivering real-time information that can significantly aid in maintaining operational efficiency.
Applications of Red Line Sight Glass
The use of red line sight glass spans various domains, each with its specific requirements and guidelines. Below are some common applications:
- Industrial Manufacturing: Used in chemical plants to monitor the level of volatile fluids.
- Water Treatment Facilities: Provides clear visibility of water levels, essential for maintaining quality control.
- Food and Beverage Industry: Ensures fluid levels in processes that require strict adherence to sanitation standards.
- Home & Garden: Utilized in water tanks and decorative features to enhance aesthetic appeal.
- Fireplace Services: Monitors fuel levels in ethanol or gas fireplaces for optimal performance.
Types of Red Line Sight Glass
Different applications often necessitate different types of red line sight glass setups. Here are several common types:
1. Vertical Sight Glass
Designed for vertical tanks, this type allows for easy checking of fluid height. It is typically mounted on the side of the tank and is ideal for systems dealing with high pressures.
2. Horizontal Sight Glass
More suitable for horizontal tanks, these are designed to withstand the weight of the fluid on the glass and can be used across a variety of industries.
3. Reflective Sight Glass
Utilizes a reflective surface which enhances visibility of the fluid level. This type is particularly useful in low-light conditions.
4. Float Type Sight Glass
Employs a float to provide an accurate reading of the fluid level; it is ideal for applications where precision is vital.
Installation of Red Line Sight Glass
Proper installation of red line sight glass is essential to ensure its functionality and lifespan. Follow these basic steps for installation:
1. Plan Your Setup
Assess the area where the sight glass will be installed. Take measurements to choose the right size and type that fits your needs.
2. Prepare the Mounting Area
Ensure the mounting area is clean, dry, and suits the specifications required by the manufacturer to avoid future complications.
3. Install According to Manufacturer Instructions
Follow all manufacturer guidelines closely for securing the sight glass to prevent leaks and ensure safety. Utilize high-quality gaskets and fittings as needed.
4. Conduct Testing
Once installed, perform tests to confirm that there are no leaks and that the sight glass operates correctly under various conditions.
Maintenance of Red Line Sight Glass
To guarantee longevity and optimal performance, regular maintenance of your red line sight glass is imperative. Here are essential maintenance tips:
1. Regular Inspections
Schedule periodic inspections to check for wear and tear, cracks, or leaks. Early detection of issues can mitigate significant damages.
2. Clean the Sight Glass
Regularly clean the glass to ensure visibility is not obstructed by buildup or residue. Use appropriate cleaning solutions that will not damage the glass or the tank's contents.
3. Replace Damaged Components
If any damage is found during inspections, promptly replace the affected components to maintain system integrity.
4. Monitor Ambient Conditions
Be mindful of the operational environment; high temperatures and pressures can affect the sight glass. Adjust operational parameters as necessary.
Benefits of Using Red Line Sight Glass
Incorporating red line sight glass into your operations delivers numerous benefits:
- Enhanced Safety: Real-time monitoring reduces the risk of hazardous spills or leaks.
- Operational Efficiency: Enables prompt adjustments to operations, enhancing overall productivity.
- Cost-Effective: Preventative maintenance can save on costly repairs and potential downtimes.
- Improved Accuracy: Direct visual observation provides more accurate readings than other measuring methods.
Conclusion
In summary, the red line sight glass is an invaluable tool for businesses across various sectors, including Home & Garden, Glass & Mirrors, and Fireplace Services. Understanding its applications, varieties, installation procedures, and maintenance will empower your business to operate more effectively. For more information on high-quality sight glass products, visit gage-glass.com and ensure you are equipped with the best in the industry.
Frequently Asked Questions About Red Line Sight Glass
1. What is the purpose of the red line on the sight glass?
The red line serves as a visual marker indicating the optimal liquid level, allowing operators to quickly gauge fluid status at a glance.
2. Can sight glasses be used for both liquids and gases?
Yes, red line sight glass can be utilized for both liquids and gases, and their effectiveness depends on the pressure and temperature conditions of the system.
3. How often should I inspect my sight glass?
Regular inspections should be conducted at least once a month, or more frequently if the system operates under extreme conditions.